15.06.2020
5 million investment in industrial processes
A global investment of more than 5 million Euros will be invested during 2020 in the modernization of industrial processes and the utilisation of our wood resource. Enhancing our resources and optimizing our production through new investments. Investments are spread over all the Group’s sites, the objectives being to improve productivity and competitiveness through identified levers: • Modernization of services ; • Improving quality and adding value to products; • Enhancement of wood resources; • Modernization of production tools and industrial practices; • Improvement of equipment as part of a voluntary environmental approach..
When patching is done automatically
Patching consists in filling the lack of wood, such as knots, on the Maritime Pine plies, with a wood patch. The installation of a new patching line on the Sauzé-Vaussais site (79) will significantly increase the production of high grade face panels. Equipped with a latest-generation colour camera and two high-precision patching heads, it will double the site’s patching capacity. A new, more elaborate patch shape will ensure better adhesion and more discreet patching.
Machining at the forefront
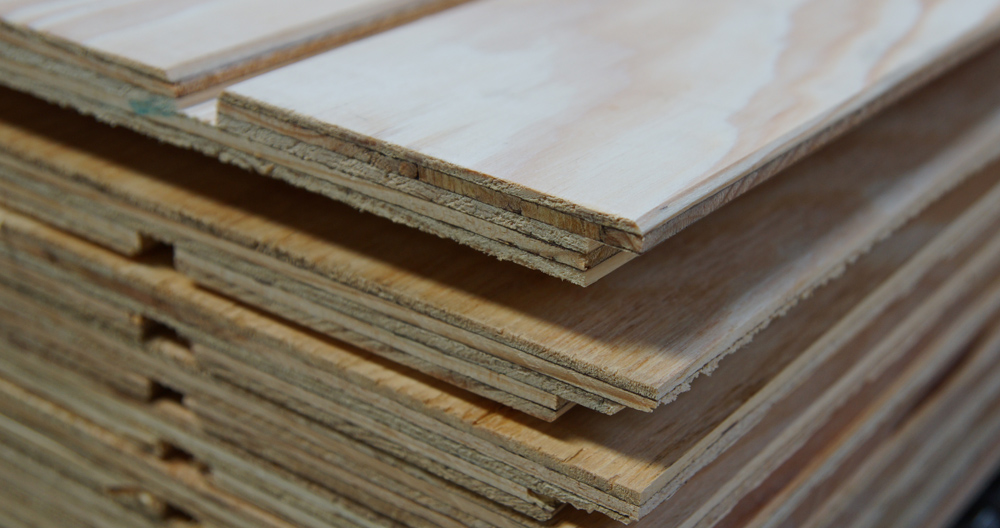
The Maritime Pine plywood peeling and manufacturing site in Solferino (40) will in turn be equipped with a high-performance machining line with multiple options, including the possibility of producing reduced strips only 300 mm wide. Fully automated, this new equipment will require no manual intervention, except for initial adjustments, and will triple the production capacity of TG machined Maritime Pine panels, such as TeboFloor or TeboRoof products for the machining of edges, raw panels or WeatherScreen treated panels.
Dimensional cutting saw
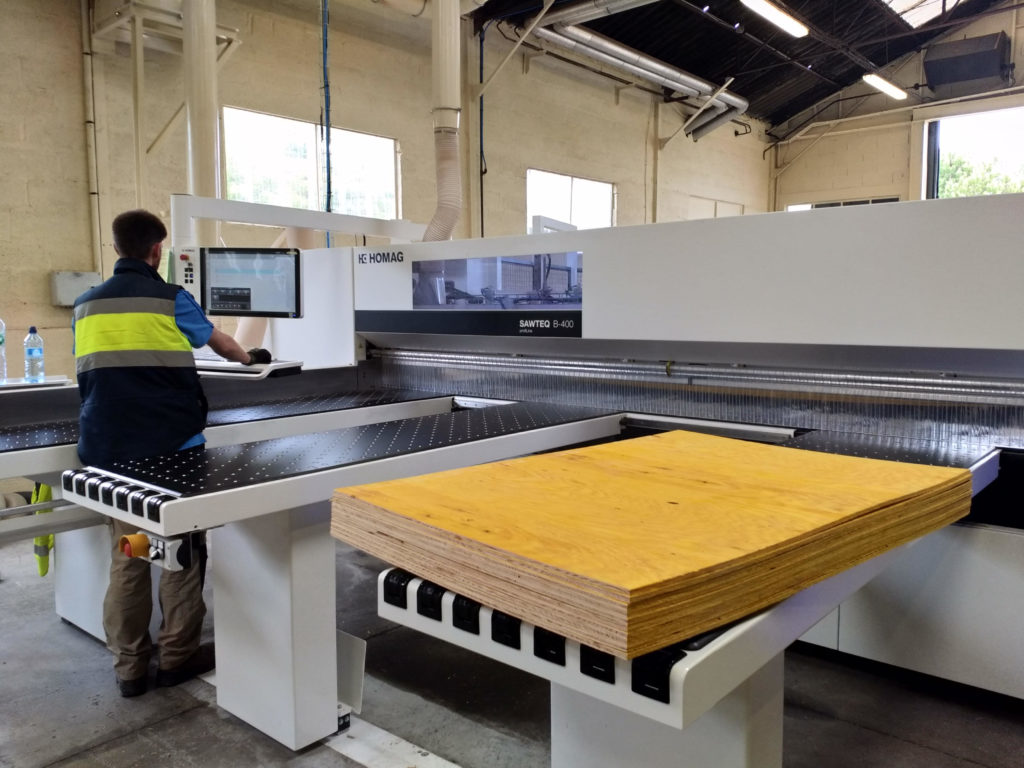
The Magné site, where Okoume and Poplar-based plywood is produced, is equipped with a high-performance cutting saw. Limiting handling, this German-designed saw, manufactured by the Homag company, combines flexibility of use with high technical precision and a capacity to cut panels up to 110 mm thick in record time in manual or automatic operation. Thanks to a specific software and in conjunction with the sales department, it offers an optimization of the cutting plans as soon as the order is received. It thus makes it possible to offer this technical service on all panels in the THEBAULT range.
The electrostatic filter
The electrostatic filter is a gas dedusting device based on the operating principle of electrostatic separation. This technology is particularly efficient for the separation of the smallest particles and guarantees a very low level of dust emissions in the gases thus cleaned. The installation of this type of filter on the boiler of Solferino (40) has allowed to optimize the gas flow by improving the energy efficiency of the installation
Head Office refurbishment and extension.
The THEBAULT Group takes care of its general services by expanding its historically established head office in Magné (79). These new square meters will contribute to the modernization of the offices by bringing comfort and ergonomics to the various workstations. The reception hall will be turned into a showroom to present to visitors, suppliers and customers an example of the use of plywood in construction. Contractor: Agence AA – Niort Surface area : construction 60 m², extension 180 m² and rehabilitation 140 m² Opening: September 2020 Products used: TeboPin Wallsheathing and TeboFloor plywood for structural uses and TeboPin Elite in interior wall lining.
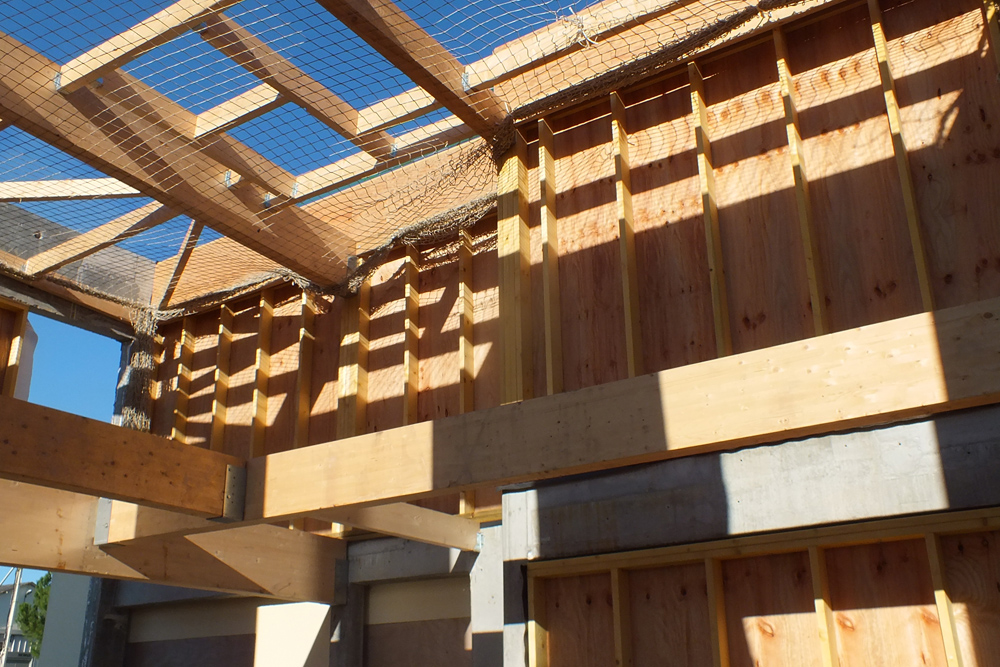
- Contractor: Agence AA – Niort
- Surface area: construction 60 m², extension 180 m² and rehabilitation 140 m²
- Opening: September 2020
- Products used: TeboPin Wallsheathing and TeboFloor plywood for structural uses and TeboPin Elite in interior wall lining.